Стандартизация
цвета и реальное цветовое
пространство во флексографской печати
Восприятие «цвета»
как цветового тона еще не подвергалось
анализу. Может ли весь процесс быть
оптимизирован (стандартизирован) для
того, чтобы учитывать и эту величину?
Следует ли добиваться стандартизации
цветового тона для серий красок таким
же образом, как это было проделано
для офсетной печати много лет назад? |
Д-р
Ганс-Якоб Кок,
Flint Group, XSYS Print Solutions
Во
всех сегментах производственной цепи печати
на упаковке ведется работа по стандартизации
процессов и их этапов, что, помимо всего
прочего, позволит осуществлять переход
от одного элемента цепи к другому на основе
четких, однозначно трактуемых, стандартизированных
данных. Это должно в итоге улучшить качество
и эффективность производственного процесса.
Соблюдение требований, установленных стандартами,
- основное условие эффективности процесса
в целом.
Печатные краски играют важную роль в
этом процессе, поскольку от них в итоге
зависит успех или крах всех усилий. Поведение
краски при передаче из камерного ракеля
на анилоксовые валы, а после на фотополимерные
печатные формы и характер восприятия краски
запечатываемой поверхностью определяются
большим количеством параметров, среди
которых центральную роль всегда играет
граничный (interfacial) эффект. Вне всякого
сомнения, даже сегодня эти процессы по-прежнему
не «контролируются», как это требуется
для стандартизации. Помимо физических/химических
переменных (поверхностное натяжение краски,
природа поверхностей анилоксового вала,
фотополимерной формы и запечатываемого
материала, силы адгезии и когезии, показатель
рН, вязкость и т. д.), существует еще
целый ряд величин, которые определяются
технологическими параметрами печатной
машины. Но, в конце концов, целью всегда
является эффективное производство упаковки,
удовлетворяющей запросы рынка. В связи
с этим восприятие «цвета» как цветового
тона еще не подвергалось анализу. Может
ли весь процесс быть оптимизирован (стандартизирован)
для того, чтобы учитывать и эту величину?
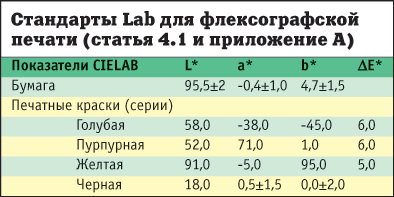
До тех пор, пока речь идет о полиграфических
красках, вопрос стоит следующим образом:
следует ли добиваться стандартизации цветового
тона для серий красок таким же образом,
как это было проделано для офсетной печати
много лет назад? Усилия в этом направлении
привели к созданию стандарта ISO/DIS 2846-5.
В этом стандарте дана спецификация приведенной
к единому виду информации по флексографскому
печатному процессу (запечатываемым материалам
и печатным краскам) (табл. 1).
Каковы преимущества
стандартизации?
Стандарты
полезны только в том случае, если они
в итоге приводят к экономическому успеху!
На всех этапах производственного процесса
цветовые координаты (Lab) могут быть точно
определены и использованы в качестве единой
спецификации для производителя красок
и типографии. В определении стандартизированных
величин, однако, следует уделить внимание
тому, что результаты печати на практике
могут в значительной мере варьироваться,
поскольку большое разнообразие используемых
материалов, их качество и другие факторы
печатного процесса тоже могут оказывать
влияние на цветовой тон. Все участники
производственной цепочки должны заранее
осознавать этот факт.

Рис.
1. Координаты голубого цвета после печати
цветопробы на
бумаге 13 разных видов в сравнении со
стандартным голубым цветом
Это становится особенно заметно, когда
проводится сравнение бумажных материалов,
широко используемых при печати на гофрокартоне
и бумажных мешках, со стандартными величинами.
Для сравнения голубая краска была нанесена
на образцы бумаги разного качества с одинаковыми
показателями передачи краски, и результат
был измерен с помощью спектрофотометра
(рис. 1). На графике хорошо видно сильное
влияние типа запечатанного материала.
В «реальном» цветовом пространстве (рис.
1, красные символы) данных видов бумаги
величина колебаний DE>5. Поскольку
каждый пользователь может оценить и одобрить
цветовой тон на бумаге «его» класса, показатели
стандартизации останутся по отношению
к заказчику на втором плане.
В связи с этим подход должен осуществляться
по двум направлениям:
- единая спецификация для стандартизированной
информации;
- определение «внутрикорпоративных»
стандартов. Это может быть, например,
наиболее часто используемый запечатываемый
материал.
В реальных условиях при печати упаковки
важны не только цветовые координаты, определяющие
выбор пигментов для краски, но и конкретные
типичные требования в производстве упаковки,
как, например:
- светостойкость;
- устойчивость к погодным условиям;
- требования производства (температура,
стерилизация и т. д.);
- механическая прочность (к истиранию
и т. п.);
- химическая устойчивость;
- цена (о ней не следует забывать!).
В зависимости от комбинации предъявляемых
требований выбор пигментов не всегда осуществляется
по цветовым координатам, но все больше
по итоговому собственному профилю, то
есть, по меньшей мере, по комбинации «цветовой
тон - физико-химические свойства - цена».
Во многих случаях невозможно достичь идентичных
цветовых координат для различных областей
применения (свойства светостойкости) просто
потому, что не существует пигментов, которые
могут эту идентичность обеспечить.
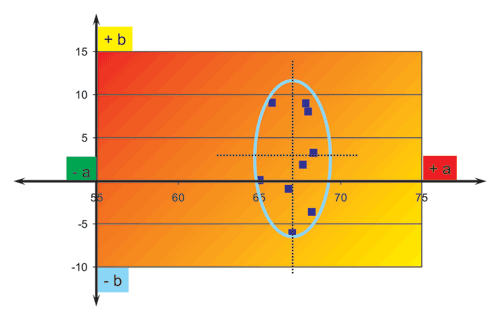
Рис.
2. Цветовые координаты пурпурной краски
(напечатано на
одном и том же материале с одной и той
же величиной краскопереноса)
В результате пурпурный цвет для сегмента
по производству мешков с большой грузоподъемностью
(высокая устойчивость к атмосферным воздействиям)
трудно сравнивать с пурпурным для розничных
ПЭ-пакетов (экономичный вариант). Это
показано на рис. 2, где приведены показатели
ассортимента пигментов, присутствующих
сейчас на рынке.
Все прошедшие измерение пигменты продаются
на рынке как пурпурные, хотя отклонения
очевидны (Da*>4 и Db*>10). Когда
используются различные типы пурпурного,
разница между цветовыми тонами может достигать
DE*>10.

Рис. 3. Кривая отражения
«идеальной» и «реальной» пурпурной краски
К сожалению, органические пигменты не
являются идеальными красящими веществами
(кривая отражения на рис. 3 - черная линия).
В зависимости от производственного процесса
области поглощения в синей и желто-зеленой
областях могут меняться, так что цветовой
тон пурпурной краски оценивается как явно
отличный от стандартного.
Для областей применения с низким уровнем
требований выбирают «наиболее дешевый»
вариант (а не определенный стандарт),
в случае наиболее высоких требований часто
приходится прибегать к «самому дорогому»
(к сожалению) - рис. 4.
Рис. 4. Стоимость пурпурной
краски в диапазоне от красного к синему
Одним из наиболее часто используемых
пигментов является пурпурный PR 57:1 -
пигмент со средним уровнем стойкости.
На рынке присутствуют различные производители
пигмента, химическая структура которого
четко определяется цветовым индексом PR
57:1. Тем не менее, цветовые тона иногда
явно различаются. В высококачественной
растровой печати в практических условиях
эти изменения цвета приводят к заметным
невооруженным взглядом изменениям в готовом
изображении. В результате взаимозаменяемость
этой пурпурной краски практически невозможна,
если только не будет изготовлен новый
комплект печатных форм.
Помимо четкой химической структуры, на
определение цветовых координат оказывают
влияние и другие факторы. Это размер частиц
и их распределение по размерам, а также
модификации поверхности в ходе процесса
производства пигментов, которые, к сожалению,
производители часто засекречивают.
К примеру, две «модификации» пурпурной
краски PR 57:1 прошли тест в повседневном
применении. Это так называемые «желтоватая
пурпурная» и «синеватая пурпурная» с равными
областями поглощения, приводящими к смещению
тона в ту или иную сторону. Различия цветового
тона на красно-зеленой оси (Da*) явно
меньше (рис. 5).
Рис. 5. Цветовые координаты
трех образцов пурпурной краски с формулой
PR 57:1
Сильное влияние смещения по сине-желтой
оси (Db*) будет продемонстрировано на
примере.
Для печати полноцветного изображения
были выбраны четыре различных серии красок,
но в ходе печати для всех четырех использовались
одни и те же коэффициенты основных цветов.
Эти четыре пигмента для пурпурной краски
создают показанные на рис. 5 отклонения
цветовых координат (сильное смещение по
шкале Db*), в то время как остальные основные
краски четырех серий отличаются незначительно.
Цветопробные оттиски четко показывают,
что сильное смещение по шкале «голубой–желтый»
различных пигментов одного и того же цветового
индекса PR 57:1 являются ключевыми для
визуального восприятия (рис. 6). При значении
Db*=4–5 изменение цветового тона дает
две или более единиц к величине DEab.
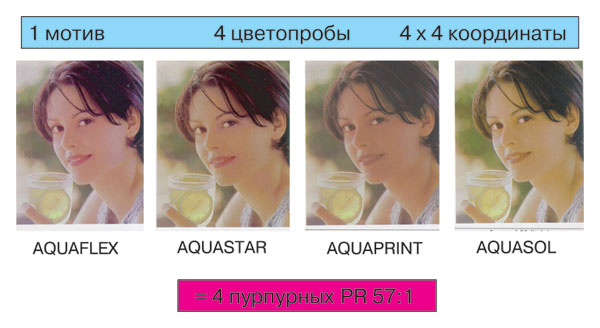
Рис.
6. Результаты четырехкрасочной растровой
печати с четырьмя
различными цветовыми координатами для
пурпурной краски (PR 57:1; Da*>4)
Подведение итогов
Результаты
явно показывают, что стандартизация требует
нескольких факторов в дополнение к одному
виду бумаги и одной системе цветовых координат.
В производстве упаковки важную роль играют
многие факторы из общего списка требований
(параметры стойкости).
В этих случаях стандартизация в первую
очередь означает, что полиграфическое
предприятие получает комплект печатных
красок, который гармонизирован со «своими»
типами бумаги и «своими» комплексами требований.
В итоге всегда получается двусторонняя
стандартизация. Это, конечно, также означает,
что на разных производствах должна быть
идентичная цветовая система - даже если
требования к ней не полностью идентичны.
На практике ситуация такова: существует
общий взаимозаменяемый набор базовых концентратов
(монопигментных составов с максимальной
концентрацией пигмента); различные требования
к механической или химической устойчивости
корректируются с помощью так называемых
разбавителей (letdowns - LDs) или технологических
составов (technology compounds - TCs).
В итоге красочная система может быть
получена путем комбинирования модульной
системы (рис. 7), состоящей из более чем
50 базовых пигментированных концентратов
(варьирование цветового тона и показателей
стабильности), а также большого количества
технологических составов и наполнителей.
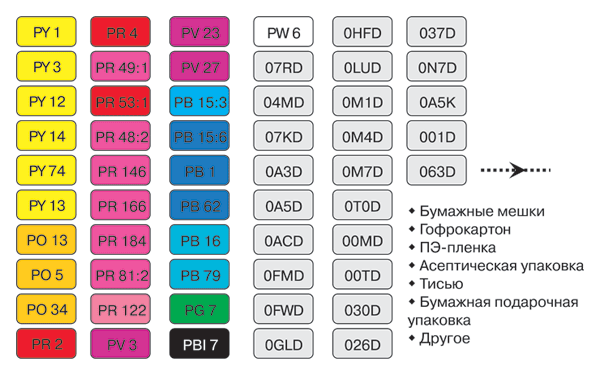
Рис.
7. Модульная система для нанесения печати
на упаковку,
состоящая из концентрата/технологического
состава/наполнителя
С помощью этой модульной системы полиграфическое
предприятие с требовательным и очень широким
спектром выполняемых работ может снизить
до минимума количество необходимых компонентов.
Свойства красок в переработке и при использовании
могут быть скорректированы с помощью специальных
наполнителей или разбавителей (см. рис.
8), например, в случае высоких требований
к параметрам скольжения или глянца.
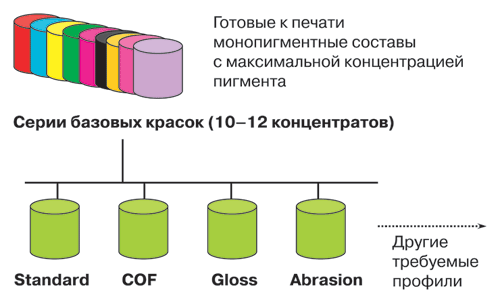
Рис. 8. Стандартная цветовая
система для различных наборов требований
Системы совместимы друг с другом, что
заметно облегчает переработку остатков
красок.

|