УФ-флексо,
офсет или высокая?
Мнение специалиста по краскам
В последнее время
в зарубежной прессе постоянно появляются
материалы, предсказывающие бурное
развитие УФ-офсетной технологии. Развитие
этого способа печати прогнозируется
не только для каких-либо специфических
задач, но главным образом как альтернатива
УФ-флексографии. То есть предсказывается
широкое распространение УФ-офсета
при печати самоклеящихся этикеток
на узкорулонных машинах. |
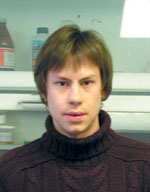 |
Андрей Малкин,
технический специалист по краскам
для узкорулонной печати,
XSYS Print Solutuons |
Конечно,
плюсы есть у любого способа печати, но не
стоит забывать и о минусах. Попробуем взвесить
все «за» и «против» и попытаемся предугадать
будущее развитие полиграфии. Из существующих
сегодня технологий узкорулонной печати
с использованием УФ-красок наиболее распространены:
- флексографская печать;
- высокая печать;
- плоская офсетная печать, или офсет.
Почти каждый серьезный производитель
печатного оборудования имеет в своей линейке
машины для различных способов печати или
даже для их комбинации.
В узкорулонной печати довольно широко
используется УФ-трафаретная печать (плоская
или ротационная). Только этим способом
можно получить очень толстый слой краски
с ярко выраженным рельефом (в среднем
10 мкм). Все остальные способы могут похвастаться
максимум 4–5 мкм. Поэтому трафарет широко
используют в комбинации с другими способами.
Например, на прозрачный материал трафаретом
наносят белила, а изображение печатают
УФ-флексо. Самостоятельно многокрасочная
трафаретная печать используется редко.
Стоимость сеток для ротационной печати
очень высока (превышает стоимость флексографских
форм в разы), поэтому если нет задачи
создать рельеф, ротационный трафарет использовать
очень дорого. У плоского трафарета формы
дешевые, но скорость печати относительно
низкая, и его использование для средних
и больших тиражей затруднительно.
Высокая печать
Стоит
отдать должное этой технологии, поскольку
именно с нее пошло развитие УФ-узкорулонной
печати. Первоначально УФ-композиции, из
которых изготавливались краски, были очень
густые, и это привело к распространению
УФ-высокой печати. Ее особенности:
- густые краски;
- сложный красочный аппарат с зональной
регулировкой (по направлению печати).
Для каждого тиража печатник настраивает
дозирование краски в зависимости от
дизайна (растр, штрих, плашка);
- твердая печатная форма с пространственным
разделением печатных и пробельных элементов;
- печатный цилиндр (противодавления)
с мягким декелем.
Офсетная печать
Исторически
этот способ развивался как попытка избавиться
от проблем высокой печати, в частности,
связанных с рельефной формой. Вот особенности
УФ- и обычного офсета:
- густые краски;
- красочный аппарат с зональной регулировкой;
- печатная форма плоская, с химико-физическим
разделением печатных и пробельных элементов.
Печатные элементы - олеофильные, смачиваются
краской, пробельные - гидрофильные,
смачиваются водой;
- в связи с этим добавляется увлажняющий
печатную форму модуль - увлажняющий
аппарат;
- изображение с формы переносится на
материал с помощью промежуточного офсетного
цилиндра с резиновым покрытием;
- печатный цилиндр (противодавления)
твердый.
Флексографская
печать
Этот
способ с использованием УФ-красок появился
относительно недавно, и связано это с
появлением жидких красок. Вот принципы
этой технологии:
- жидкие краски;
- простой красочный аппарат, краска
дозируется с помощью анилоксового вала.
Для растра, плашек, штрихов используются
различные анилоксовые валы;
- печатная форма мягкая, с пространственным
разделением печатных и пробельных элементов;
- печатный цилиндр (противодавления)
твердый.
Теперь попробуем оценить достоинства
и недостатки элементов печатных машин
и материалов для этих способов печати.
Краски
Здесь
все просто. Мы, XSYS Print Solutions,
как производитель печатных красок можем
заявить, что все УФ-краски на оттисках
имеют сходные показатели (цвет, насыщенность,
стойкостные характеристики, адгезия) независимо
от способа печати. Все различия в красках
определяются как раз способом печати и
оборудованием. Флексо - жидкие, для высокой
печати и офсета - густые. Поскольку в
офсете есть промежуточная передаточная
поверхность (офсетный цилиндр), краски
должны быть более насыщенными и адекватно
себя вести при взаимодействии с увлажняющим
раствором (не эмульгировать, не свертываться
и т. д.)
Красочный аппарат
Для
высокой и офсетной печати они почти аналогичны.
Это сложное многовалковое устройство с
зональной регулировкой, что является большим
плюсом по сравнению с флексографией. Высоким
и офсетным способом можно печатать в одной
секции и очень насыщенную плашку, и тонкий
растр, и штрихи одновременно. Такой красочный
аппарат позволяет выполнять так называемый
ирисный раскат - он часто используется
при печати ценных бумаг, акцизных марок.
Однако минусов у красочных аппаратов высокой
и офсетной печати тоже немало:
- длительность настройки зональной
подачи краски;
- так называемое шаблонирование (появление
на оттиске теневого изображения);
- возможность разнооттеночности оттисков
в одном тираже;
- длительная очистка, смывка краски;
- существенные затраты на обслуживание
и замену красочных валиков;
- поскольку этот модуль сложный, значит,
и машина будет существенно дороже флексографской;
- высокое энергопотребление.
А что хорошего у флексографских красочных
аппаратов? Как мы говорили, краска дозируется
анилоксом. Это, в целом, очень удобно:
в зависимости от дизайна на ту или другую
секцию мы ставим свой анилокс с определенной
подачей краски и можем печатать - дозирование
краски настроено. Здесь нет шаблонирования
и разнооттеночности, как в высокой и офсете.
Этот модуль быстро мыть, обслуживание
простое. С другой стороны, есть и ряд
минусов:
- так как дозирование постоянное, зачастую
приходится разносить растр и плашку
на разные печатные секции. Растр требует
высокой линиатуры анилокса, а значит,
низкой подачи, а плашка - наоборот;
- анилокс - высокотехнологичный продукт,
поэтому дорогой. В среднем на семикрасочную
машину нужно 12–15 анилоксов;
- вдобавок анилоксы не вечные, и их
нужно чистить и регулярно заменять.
Печатные формы
Не
будем пытаться сравнивать тиражестойкость
и себестоимость форм для разных способов
печати. Отметим, что офсетные формы изготавливаются
быстрее всего. Но при печати этикетки
особая оперативность не нужна, да и развитие
технологии позволяет изготавливать флексографские
формы достаточно быстро.
Формы высокой и флексографской печати
похожи, а вот офсет существенно от них
отличается. Печатная форма здесь плоская,
печатные элементы имеют разную смачиваемость.
Для того чтобы на пробельные элементы
не ложилась краска, их закатывают увлажняющим
раствором, который подает увлажняющий
аппарат. А это - очередное усложнение
печатной машины. Кроме того, возникает
такая «головная боль», как поддержание
водно-красочного баланса, что требует
от печатника большого опыта.
Печатная пара
Как
известно, создание нужного давления в
печатной паре - одно из самых важных условий
получения качественного оттиска. Любые
материалы, по которым мы печатаем, на
микроуровне неровные. Натиск (давление)
нам нужен для равномерной пропечатки всех
элементов изображения. Вопрос состоит
в том, как компенсировать эти неровности.
В высокой печати используют мягкий цилиндр
противодавления, во флексографии мягкая
сама форма плюс демпфирующая монтажная
лента, в офсете компрессионным материалом
является резина офсетного цилиндра.
Так как у флексографии и высокой печати
печатные элементы имеют пространственное
разделение, часто бывает трудно добиться
равномерного натиска по всей полосе контакта
в печатной паре. Для равномерной пропечатки
плашки нужно большее давление, а если
мы с этой же формы печатаем растр, это
может привести к повышенному растискиванию.
В этом плане плоская офсетная печать
не зависит от характера печатаемого изображения.
Печатные и пробельные элементы на одном
уровне, давление по всей полосе контакта
одинаковое - это и является одним из главных
преимуществ. Например, именно поэтому
широкое распространение УФ-офсет получил
в печати картонной упаковки, в том числе
и молочных пакетов.
Иногда преимущества промежуточного (офсетного)
цилиндра используются в комбинации с формой
высокой печати - это так называемый типоофсет.
Итог
Если
говорить о качестве печати всеми тремя
способами, то офсетную печать можно считать
безоговорочным лидером. Затем идет высокая
печать, затем флексография. Преимущества
здесь кроются как раз в специфике каждого
способа. С другой стороны, постоянное
развитие технологии, разработка новых
формных материалов позволили флексографии
выйти на сопоставимый с обоими конкурирующими
способами уровень качества. Если же говорить
о производительности, то здесь, наоборот,
преимущества у флексографии, поскольку
скорость печати все-таки выше и времени
на приладку тратится меньше, а стабильность
печатного процесса самая высокая. Таким
образом, можно суммировать:
- офсетная печать дает высокое качество;
- у флексографии высокая стабильность
печатного процесса и оперативность;
- высокая печать по совокупности показателей
находится между флексографией и офсетом.
Помимо технологии, безусловно, нужно
учитывать и экономические показатели каждого
способа печати.
Если поставить вопрос, какой способ печати
самый лучший, наверное, никто с уверенностью
на него не ответит. Все способы печати
имеют право на существование и развитие,
у каждого есть свои плюсы, неповторимые
преимущества и недостатки.

|