С
чего начинается качество, или Внедрение
результатов
тестирования на производстве (Часть 3)
В первой и второй
частях статьи, опубликованных в «Флексо
Плюс»№ 4 и 5 за 2002 г., предложена
методика тестирования и профилирования
флексографского печатного процесса,
разработанная на опыте российских
предприятий, и принципы управления
качеством. В третьей, заключительной
части автор рассматривает вопросы
практического внедрения результатов
тестирования. |
|
Дмитрий Белкин, инженер
по цвету, компания
«Тампомеханика»
|
В
третьей части статьи рассмотрены вопросы,
связанные с внедрением результатов тестирования
печатного процесса непосредственно на
производстве, в цеху. По сути, как уже
упоминалось ранее, главное, на что направлены
данные мероприятия - развитие и модернизация
систем управления и контроля качества
(СКК) на производстве. Основой для построения
любой СКК служат стандарты и другие нормативные
акты, существующие в различных отраслях
промышленности, однако по причине отсутствия
действующего стандарта на флексографскую
печать компаниям, использующим данную
технологию, приходится заниматься подготовкой
внутренних стандартов предприятия (СТП),
основная часть которых как раз и формируется
по результатам тестирования печатного
процесса (ТПП).
Мы уже рассмотрели в предыдущей части
статьи («Флексо Плюс» № 5–02) основные
аспекты внедрения результатов ТПП в подразделениях
допечатной подготовки. В связи с этим
хотелось бы обратить внимание на следующее:
по сравнению с допечатным печатное производство
- процесс с большим количеством различных
технологических операций, управление и
контроль которыми осуществляется множеством
специалистов различной квалификации, а
поэтому и подход к реализации поставленной
задачи должен быть более фундаментальным.
Внедрение результатов ТПП и построения
СКК на производстве - трудоемкий и длительный
процесс, рассмотрение которого не может
быть ограничено лишь сугубо технологическими
аспектами.
Внедрение результатов
тестирования
Рис. 1. Пример
расположения контрольных элементов на
тестовом макете (слева) и на коммерческом
заказе (слева)
Доклад на производстве.
Первое, с чего желательно начинать внедрение
- это подготовка и проведение доклада
в цехе технологической службой (технологом)
о результатах, достигнутых в процессе
тестирования печатного процесса. Здесь
полезно рассказать о проблемах, которые
были обнаружены в процессе тестирования,
как протекал процесс, сколько времени
было потрачено на приладку и получение
первых нормализованных оттисков, а также
продемонстрировать диаграммы стабильности
краскопереноса в различных участках оттиска
на разных этапах печати тиража, графики
градационных характеристик, цветового
охвата. Неплохо провести сопоставление
данных, полученных при работе на различных
материалах, красках, анилоксах, режимах
и т. д. - все, что было протестировано
и изучено.
Ознакомиться с этой информацией будет
полезно технологам, печатникам, колористам
и другим ключевым специалистам и руководителям
производственных подразделений. Важно,
чтобы все эти сотрудники с первых шагов
были вовлечены в процесс внедрения и построения
СКК - или хотя бы имели представление
о нем.
Никакие административные меры, приказы,
дисциплинарные взыскания не смогут обеспечить
быстрого и эффективного достижения намеченной
цели, если не будет всеобщего понимания
и поддержки происходящих процессов - это
факт, с которым неоднократно приходилось
сталкиваться автору.
Технологические
инструкции, документация. Сегодня
к написанию инструкций многие относятся
с большим недоверием: «кто их будет читать»,
«сколько всего надо описать», однако при
всех своих кажущихся недостатках это необходимая
составляющая СКК. В частности, в инструкциях
должно быть четко оговорено, кто за что
отвечает и какие контрольные функции выполняет.
Бытует справедливое утверждение: когда
все контролируют всё, есть большая доля
вероятности, что какие-то параметры не
проверит никто, попросту понадеявшись
на другого.
Вся рабочая документация (формуляры,
бланки) должна быть подготовлена таким
образом, чтобы каждый специалист имел
доступ только к той информации, которая
необходима ему для проведения контрольно-проверочных
операций.
Предварительная
подготовка макета. На стадии допечатной
подготовки в макет вносят специальные
контрольно-тестовые элементы. Как правило,
их стараются размещать на технологических
или обрезных полях рабочего рулона или
же в малозаметных участках коммерческой
продукции: в донных или иных складках,
в швах, на второстепенных поверхностях
упаковки. Пример контрольно-тестовых элементов
и их расположения приведен на рис. 1.
Для повышения оперативности проведения
контроля качества печатных форм, а также
с целью облегчения последующей идентификации
полезно вносить в макет некоторую служебную
информацию: номер заказа, его краткое
наименование, коэффициент дисторсии, наименования
красок по сепарациям, параметры растрирования
- линиатура и углы наклона, наименование
рабочего ICC-профиля. Причем весь объем
информации, кроме наименований красок,
лучше окрашивать в цвет registration,
чтобы она присутствовала на всех сепарациях.
Контрольно-тестовые элементы активно
используются с первых этапов производственного
процесса: для контроля качества цветоделенных
диапозитивов (негативов), затем печатных
форм, монтажа и, наконец, непосредственно
печатного процесса и тиражных оттисков.
Построение системы
контроля. Чтобы иметь четкое представление
обо всех контролируемых параметрах как
самого производственно процесса, так и
промежуточной и конечной продукции, полезно
составлять сводные каталоги-таблицы этих
параметров. При этом, рассматривая каждую
производственную операцию в отдельности,
необходимо различать следующие виды контроля:
- контроль принимаемых материалов и
сырья;
- контроль производственного процесса;
- контроль выпускаемой продукции.
В качестве примера такой таблицы приводится
операция изготовления фотоформ, а именно
процесс выходного контроля продукции.
На производствах с большим ассортиментом
выпускаемой продукции удобно различать
эту продукцию по критериям сложности выполняемых
работ - это позволит ввести более гибкий
контроль, не предъявляя завышенных требований
к простым работам. На основе этого каталога
готовятся технологические инструкции по
всем операциям.
|
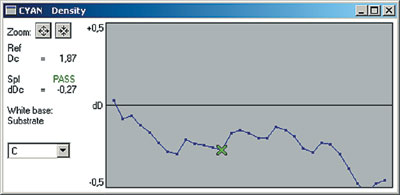 |
Рис. 2. Графики стабильности воспроизведения
оптических плотноcтей в рамках одного
тиража
по черной (вверху) и пурпурной (внизу)
краскам
|
В процессе тестирования производственного
процесса и изучения тестовых оттисков
мы определили основные контролируемые
параметры и характеристики и зафиксировали
их значения. Затем, в ходе проведения
исследований полученных результатов, были
установлены допуски на значения этих параметров
и характеристик в соответствии с интервалами
варьируемости. Под интервалом варьируемости
понимается реальный разброс измеренных
(оцененных) значений. Допуск не может
быть меньше рабочего интервала варьируемости,
более того, желательно, чтобы он был несколько
больше.
Однако не все характеристики можно измерить.
В связи с этим различаются две категории
параметров:
- переменные параметры - выражаются
в числовых значениях (скорость печати,
вязкость красок, параметры анилоксов,
поверхностное натяжение запечатываемого
материала, приводка и т. д.);
- качественные признаки - не поддаются
числовому выражению, работают по принципу
«проходит - не проходит» (полошение,
марашки, дробление, двоение, муар, соответствие
цветопробе).
Для контроля качественных признаков применяют
метод визуальных сравнений с эталонами,
демонстрирующими приемлемое и неприемлемое
качество продукции. В нашем случае эталонами
являются тестовые оттиски, а основным
ориентиром в плане общей качественной
оценки оттиска для печатника является
цветопроба.
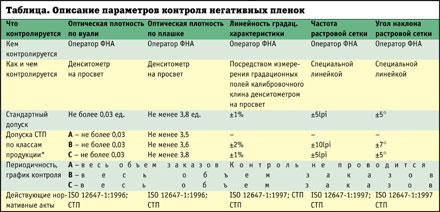
*
В данном случае классам соответствуют
следующие параметры продукции:
A - простые плашечные работы без растра
и мелких деталей;
B - растровые работы с линиатурой 60 lpi
без мелких деталей;
С - растровые работы с высокой линиатурой
до 150 lpi
и мелкими деталями
|
Рис. 3. Настройка предельно допустимых
отклонений цветового тона |
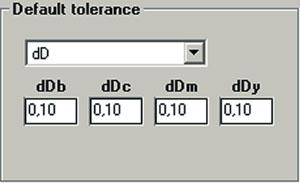 |
Рис. 4. Настройка предельно допустимых
отклонений оптических плотностей
|
Процесс печати.
Используемые средства и методы
контроля во флексографии столь разнообразны
и многочисленны, что, к сожалению, описать
их все в рамках данной статьи не представляется
возможным. Поэтому автор хотел бы рассмотреть
лишь те из них, которые наиболее актуальны
с точки зрения профилирования печатного
процесса.
Рассмотрим прежде, какие же основные
материалы и их свойства являются исходными
для печатного процесса:
- фотополимерные
печатные формы: толщина по нескольким
точкам, твердость по Шору А, равномерность
воспроизведения различных элементов
по площади формы, устойчивость к различным
средам, технология изготовления - аналоговая/цифровая,
строение - однослойная/многослойная;
- двусторонний
скотч: толщина и допуск на разнотолщинность,
твердость по Шору А, сила адгезии к
форме, цилиндру или гильзе;
- запечатываемый
материал: толщина, белизна, глянец,
впитывающий/невпитывающий, поверхностное
натяжение;
- печатные краски:
вязкость, метод сушки или закрепления,
оптическая плотность, отражаемый спектр
(две последние характеристики могут
быть оценены лишь после нанесения краски
на запечатываемый материал);
- контрактная
цветопроба (изготавливаются три копии:
заказчику, на производство, в архив):
примененный профиль, материал-носитель,
технология изготовления - аналоговая
или цифровая, полутоновая или растрированная.
Подразумевается, что все вышеописанные
материалы успешно прошли входной контроль
и приемку продукции на соответствующих
производственных стадиях, и их свойства
и характеристики соответствуют стандартным
параметрам в рамках СТП, а также подобраны
в полном соответствии с условиями ТПП.
Необходимо упомянуть об оснастке самой
печатной машины: формных цилиндрах или
гильзах, анилоксовых валах, ракельных
полотнах.
|
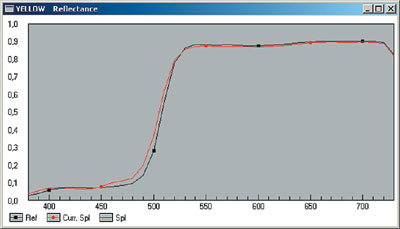 |
Рис. 5. Сопоставление спектральных
характеристик отражения
эталонного (тестового) и коммерческого
оттисков по
голубой (вверху) и желтой (внизу)
краскам |
После того, как печатная машина «заряжена»,
то есть выполнены все подготовительные
операции, начинается приладка. На этой
стадии происходит наиболее активное использование
результатов, полученных при проведении
тестирования. Все режимы, параметры и
свойства процесса должны быть изложены
в технологической карте, по которой печатник
настраивает печатную машину.
После проведения предварительной приладки
наступает момент Х - когда печатник сопоставляет
полученный оттиск с цветопробой. Для проведения
таких контрольных операций желательно
иметь источник нормализованного освещения
D65 и проверить печатников на отклонение
от средней нормы зрительного восприятия.
Существует специальный стандарт ISO/CIE
10527:1991 «Наблюдатели, отвечающие требованиям
стандартов МКО (Международной комиссии
по освещению) для работы в области колориметрии».
В том случае, если результат сопоставления
оттиска и цветопробы положительный, работа
по окончательной отладке процесса продолжается
дальше. Если же обнаруживаются значительные
отличия от эталона, то в оперативном порядке
проводятся измерения контрольных шкал,
полученные данные сопоставляются с результатами
измерений эталонных оттисков и анализируются.
По результатам анализа вырабатываются
рекомендации, направленные на нормализацию
печатного процесса.
Для проведения контрольных измерений
используются денситометр или спектрофотометр.
Главное - в целях обеспечения повторяемости
для контроля должен использоваться один
и тот же прибор. На практике показания
различных приборов могут существенно различаться.
Значительно облегчает и ускоряет процесс
контроля и анализа использование специального
программного обеспечения. Такие программы
позволяют:
- создавать базы данных измерений эталонных
оттисков;
- получать максимальное количество информации
о характеристиках цвета в числовом и
графическом представлении;
- вводить размеры допусков на контролируемые
значения;
- проводить анализ, вплоть до выдачи
рекомендаций;
- накапливать статистическую информацию
о всех проведенных контрольно-измерительных
операциях.
Если такой программы нет, можно просто
подключить измерительный прибор к компьютеру
с последующей передачей данных через интерфейсную
программу в любые приложения Excel, Word
и др. Как правило, все модели современных
спектрофотометров и денситометров имеют
интерфейсные выходы, правда, не всегда
в стандартной поставке имеется кабель
для подключения.
Если же на вашем производстве пока нет
таких приборов, то можно вполне эффективно
проводить визуальный контроль посредством
сопоставления шкал коммерческого и эталонного
оттисков.
После того, как требуемое качество достигнуто,
необходимость в проведении контроля остается,
но теперь, по сравнению с предыдущими
производственными операциями, мы лишены
возможности контролировать каждую единицу
продукции, поэтому производится выборочный
контроль. Для него готовятся выборки образцов
продукции, но этот процесс не должен быть
хаотичным. Процедура подготовки выборок
подробно описывается в стандарте ISO 2559.
Основные рекомендации заключаются в следующем:
- никогда не составляйте выборку из
одной части тиража;
- отбирайте образцы по возможности из
всех частей тиража;
- количество образцов должно соответствовать
объему тиража, то есть чем больше тираж,
тем больше образцов следует взять в
выборку.
Проверка работоспособности
системы и внесение корректировок. Перед
внедрением СКК очень полезно провести
ее пробную обкатку. Желательно подготовить
специальный контрольно-тестовый макет.
Тут можно от души поэкспериментировать
с различными установками цветоделения.
Если останется место, можно вставить блоки
полей с равномерной проработкой различных
цветовых диапазонов - что-то наподобие
цветовых атласов.
Если все пройдет хорошо, вы будете спокойны
за последующие результаты. Если же возникнут
какие-то отклонения, вы сможете их оценить
и учесть, и снова будете спокойны.
Заключение
Завершая
обзор по технологиям тестирования, профилирования
и стандартизации печатного процесса во
флексографии, разработка которых еще далеко
не закончена, автор не хотел бы ставить
точку и приглашает читателей к обсуждению
этой темы на форумах www.flexoplus.ru
и www.tampomechanika.ru.

|