Лазерное
гравирование
цилиндров глубокой печати
В предыдущем номере
журнала мы рассмотрели тему гравирования
цилиндров глубокой печати электромеханическим
способом. Столкнувшись с многими проблемами
при совершенствовании принципа электромеханического
гравирования, крупнейшие производители
формного оборудования обратили свой
взгляд на возможность использования
лазера при изготовлении цилиндров
глубокой печати. В этой статье мы
продолжим тему гравирования и рассмотрим
самые современные лазерные технологии. |
|
Дмитрий Тараненко,
издательство «Курсив»
|
Безусловно,
первое, что приходит в голову, когда полиграфисты
слышат о лазерном гравировании в глубокой
печати - это использования лазера для
непосредственного гравирования по меди.
В этом случае весь технологический процесс
большинства предприятий, использующих
электромеханическое гравирование, не пришлось
бы изменять. Достаточно было бы установить
вместо привычного «Гелиоклишографа» новую
систему - и все. Но, к сожалению, такое
простое решение до сих пор не нашло практического
применения - уж очень высокие мощности
лазера необходимы для реализации его принципов.
К тому же большие затраты электроэнергии
серьезно влияли бы на конечную стоимость
гравированного цилиндра.
Лазерное гравирование:
первые попытки
Применение
лазеров дает массу преимуществ, включая
высокую скорость и стабильность процесса.
Но даже сейчас из-за малой мощности лазеров
невозможно реализовать на должном уровне
гравирование медного покрытия из-за его
большой теплопроводности. Самая главная
причина - необходимость в получении лазера
огромной мощности, что требует больших
энергозатрат, да и к тому же быстродействие
будет уменьшаться пропорционально росту
мощности.
Комментарий
редакции
История
травления: основные методы
Рассмотрение
методов изготовления форм глубокой
печати, особенно косвенного гравирования
было бы не полным без изложения
истории развития и основных принципов
травления медного слоя.
Существует несколько способов получения
копии на формном цилиндре с помощью
травления, каждый из которых отличается
операциями, качеством и конфигурацией
печатающих элементов:
- Классический
способ с применением пигментной
бумаги. Пигментная бумага представляет
собой желатиновый слой (около
40–60 мкм), нанесенный на бумажную
подложку. В желатиновый слой диспергирован
пигмент (обычно Fe2O3), придающий
слою коричнево-красный окрас.
Перед применением такая бумага
требует сенсибилизации (обычно
в бихромате калия K2Cr2O7), после
чего на пигментную бумагу экспонируют
сначала растр (плоскопараллельная
стеклянная пластина, на которой
расположены темные, непрозрачные
квадраты, разделенные узкими прозрачными
линиями с линиатурой до 120 лин/см),
а затем полутоновый оригинал (диапозитив).
После этого по тонкому слою ламинарно
стекающей по цилиндру воды копию
на пигментной бумаге прикатывают
желатиновым слоем к медной поверхности
цилиндра. Затем в специальном
проявочном устройстве происходит
проявка в воде, и бумажная подложка
легко отделяется. Проявленную
копию промывают холодной водой,
высушивают спиртом, обдувают воздухом,
после чего приступают к травлению.
Желатиновый слой, оставшийся после
проявки на цилиндре, создает на
его поверхности рельефное изображение,
и именно этот рельеф регулирует
глубину травления печатающих элементов.
Травление осуществляется раствором
хлорного железа - FeCl3. Травящий
раствор вызывает набухание пигментно-желатинового
слоя и проникает (диффундирует)
к поверхности меди, вступая с
ней в химическую реакцию, в результате
чего медь растворяется пропорционально
нанесенному желатиновому слою.
Под тонкими участками слоя травление
начинается раньше и протекает
интенсивнее, чем под более толстыми
слоями. Управляя условиями травления,
можно управлять градацией тонов
изображения. До появления автоматических
травильных комплексов использовалось
так называемое ручное многоступенчатое
травление, так как только такой
способ мог дать возможность пропорциональной
передачи тонов. Поэтому травление
производилось последовательно
четырьмя-шестью растворами убывающей
концентрации. При таком подходе
качество изображения напрямую
зависело от опыта и уровня подготовки
мастера-травильщика, а кроме того,
требовалось наличие в линии нескольких
ванн, каждой со своей концентрацией.
Глубина ячеек - от 3 мкм в светах
и 35 мкм в тенях.
Позднее стали появляться автоматические
станции травления, основанные
на двух принципах:
- в первом случае, как и в
ручном способе, использовались
различные концентрации FeCl3,
причем управление процессом
было целиком автоматизировано
и позволяло задавать различные
комбинации обработки цилиндров;
- во втором случае использовалась
только одна концентрация хлорного
железа, но с применением специальных
добавок. Градационную передачу
здесь можно контролировать
с помощью скорости вращения
цилиндра, температуры и концентрации
раствора (например, это было
осуществлено в системе «Контромат»).
В любом случае системы оборудованы
устройствами обратной связи,
позволяющими непрерывно контролировать
глубину травления и вносить
соответствующие коррективы.
Существенным недостатком такого
способа получения формного цилиндра
глубокой печати является трудность
обеспечения заданных размеров
бумажной подложки на протяжении
всех операций, связанных с ее
обработкой. Кроме того применение
многих химических растворов
делало весь процесс получения
формы трудоемким и достаточно
сложно контролируемым.
- Глубокая
автотипия. Идея автотипного
растрирования в глубокой печати
почти также стара, как и сама
глубокая печать. Однако все попытки
ее реализовать не увенчались успехом
вплоть до изобретения специального
растра. Пленочный комбинированный
полутоновый контактный растр состоит
из непрозрачных линий, пересекающихся
под прямым углом (наличие таких
линий обеспечивает создание пробельных
элементов для опоры ракеля), а
в квадратах между прозрачными
линиями оптическая плотность от
минимальной в центре возрастает
к краям (так же как и в применявшемся
ранее контактном растре для офсетной
печати).
Сам процесс получения печатной
формы, по сравнению с так называемым
традиционным, технологически проще,
быстрее и экономичнее. Заключается
он в следующем: изготавливается
растровый диапозитив полутонового
оригинала, после чего происходит
его копирование на предварительно
нанесенный на медную поверхность
цилиндра тонкий (3–4 мкм) копировальный
слой. Наибольшего развития в то
время достиг способ нанесения
копировального слоя на цилиндр
с помощью поливного кольца и в
случае с небольшими цилиндрами
- центрифугирования. Сам диапозитив
крепился либо очень надежным вакуумным
способом, либо способом натягиваемой
пленки.
При использовании глубокой автотипии,
кроме обычного травления с помощью
хлорного железа, стало возможно
еще и электролитическое травление,
позволяющее достигать более высоких
результатов в управлении процессом.
- Полуавтотипная
глубокая печать. Процесс
напоминает травление с применением
пигментной бумаги, однако имеет
и свои отличия: для изготовления
копии на светочувствительном материале
(кроме пигментной бумаги использовались
еще и такие марки материалов,
как «Аутофильм» и «Ротаргофильм»,
отличающиеся меньшей деформацией
в процессе копирования) использовалось
двойное экспонирование, заключающееся
в последовательном экспонировании
сначала полутонового позитива,
а затем и растрового, что позволяло
регулировать тонопередачу изображения.
Еще одним отличием является и
возможность травления при использовании
только одного раствора заданной
концентрации. Однако при двойном
экспонировании, помимо основных
возможных погрешностей в технологии,
существует увеличенная, по сравнению
с одинарным, вероятность неприводки.
Для устранения этой проблемы были
предприняты неоднократные попытки
ввести технологию изготовления
только одного диапозитива (например,
галогеносеребрянной пленки - «Ротофильм»),
однако они так и не получили распространения
ввиду непропорционального возрастания
стоимости процесса.
Отдельно стоит отметить и отличие
формы и конфигурации ячеек во
всех трех способах:
- результатом традиционного
способа печатающие элементы
имеют одинаковую для всех
деталей изображения площадь,
но разную глубину - меньшую
в светах и большую в тенях;
- в глубокой автотипии все
печатающие элементы имеют
одинаковую глубину, но различную
форму поверхности;
- при полуавтотипной глубокой
печати объем печатающих элементов
определяется и поверхностью,
и глубиной.
|
|
Примерный вид изображения,
полученного на цилиндре
с помощью установки Digilas
|
Если же говорить об истории, то наиболее
интересное решение, реализующее лазерное
гравирование, было представлено в 1983
г. компанией Crosfield (Великобритания),
приобретенной впоследствии компанией FujiFilm.
Это комплексное решение под названием
Lasergravure 700 в полной мере позволяло
использовать преимущества цифровой подготовки
полос, а кроме того, включало в себя все
операции вплоть до никелирования готовой
формы для увеличения тиражестойкости.
Сущность технологии изготовления цилиндров
в этой системе заключается в следующем:
на предварительно отрастрированный (травлением
или гравированием) омедненный цилиндр
методом электростатического напыления
наносится порошок эпоксидной смолы, который
прочно фиксируется за счет последующей
термообработки. В результате образуется
тонкий (до 50 мкм) блестящий слой, который
после шлифовки гравируется CO2-лазером.
На заключительной стадии наносится тонкий
слой никеля, чем и достигается тиражестойкость
до 3 млн оттисков. Этот способ обеспечивал
небывалую для того времени производительность
- гравирование цилиндра длиной 1,6 м с
длинной окружности 1200 мм занимало около
33 мин. Кроме того, возможно было повторное
(до 10 раз) использование цилиндра. Отличительной
особенностью такого гравирования является
овальная форма ячеек.
|
Установки косвенного лазерного гравирования:
HelioBeam C2000 (вверху) и Digilas
3500 (внизу) |
Были и другие попытки использования лазера
для гравирования: например, использование
в качестве гравируемой поверхности листовой
или рукавной пластмассы, обеспечивающей
необходимую тиражестойкость и закрепляющейся
на цилиндре при помощи термообработки.
В этом случае привычных ячеек уже не было
- на их месте можно увидеть непрерывные
спиральные линии.
Однако все эти способы сегодня практически
не применяются, им на смену пришли две
новые технологии: использование для гравировки
масочного слоя и дальнейшее его травление
(компания Hell) и прямое лазерное гравирование
предварительно нанесенного на медный цинкового
слоя (компания Daetwyler).
Косвенное лазерное
гравирование
В
начале 90-х гг. был совершен очередной
прорыв в использовании лазера в глубокой
печати - впервые был реализован масочный
(косвенный) метод. При косвенном лазерном
гравировании омедненный цилиндр покрывается
тонким слоем черного вещества (если следовать
аналогии с более ранними советским разработками
в полиграфии, то скорее всего применяемое
вещество представляет собой покрытие,
состоящее из угля и стойкого к травлению
полимера), которое испаряется низкомощным
(60 Вт) многорежимным Nd:YAG-лазером (разработка
велась компанией Spectron в сотрудничестве
с Schepers-Ohio), снабженным внешним акусто-оптическим
модулятором. В дальнейшем проводилось
травление (выборочность которого обеспечивалась
предыдущей стадией), после чего для увеличения
тиражестойкости - хромирование. Форма
ячеек, полученная таким методом - полусферическая,
что обеспечивает хорошую передачу краски.
В то же время подобным процессом травления
достаточно сложно управлять в должной
мере. Из проблем, стоящих при использовании
травления, можно назвать, во-первых, недостаточно
точный контроль глубины ячеек, а во-вторых,
подтравливание стенок ячеек (что можно
решить, например, введением ПАВ в травильный
раствор). Стоимость же установок, обеспечивающих
действительно полный контроль над травлением,
в то время была очень большой.
|
Японский прототип установки косвенного
лазерного гравирования LaserSream
|
На текущий момент на рынке представлено
несколько подобных решений:
- компания MDC
Max Daetwyler производит двухлучевую
систему лазерного гравирования Digilas
3500 с диаметром луча 20 мкм и мощностью
YAG-лазера в 100 Вт. Опционально возможно
использование и 10 мкм аппертуры (5080
dpi). Модель предназначена для цилиндров
или рукавов диаметром от 50 до 500 мм,
длиной до 2032 мм и снабжена автоматической
системой балансировки во время гравирования.
Для подготовки цилиндров к гравированию
используется наносимый мелкими брызгами
в специальной установке (Spray Coater)
специальный черный лак (определенной
толщины), после чего необходима сушка
в течении 5 мин. Для обеспечения требований
экологии система снабжена необходимыми
фильтрами и вытяжками. Флагманом моделей
для нанесения лакового покрытия является
Spray Coater 7100-85, позволяющая обрабатывать
цилиндры весом до 7,5 т, диаметром до
850 мм и длиной до 730 см.
После того, как лаковое покрытие подверглось
гравированию, наступает стадия травления.
На этом этапе регулируется скорость
вращения и осцилляции, время травления.
После травления происходит смывка водой
остатков травления и обезжиривание поверхности
с последующим хромированием;
- установка HelioBeam
C2000, производимая компанией
Hell. Основной элемент - волоконный
лазер мощностью 60 Вт, работающий на
длине волны 1110 нм. Гравирование ведется
восьмью параллельными лазерными пучками.
Диаметр лазерного луча 5–10 мкм. Воспроизводимая
линиатура - 60–140 лин/см (возможно
использование линиатуры 200 лин/см при
разрешении 5080 dpi). Установка позволяет
обрабатывать цилиндры весом до 500 кг,
длиной 400–2000 мм и окружностью до
1200 мм. Установка снабжена системой
автоматической балансировки. Кроме всего
прочего, оператор такой установки не
привязан к традиционной форме ячеек
- в поставку включены программные средства
для задания конфигурации растровой точки;
- установка LaserStream,
разрабатываемая японской компанией Think
Laboratory. На текущий момент прототип
установки уже готов, но сведений о свободной
продаже пока нет. В установке используются
лазерные головки компании Creo. По заявлению
разработчиков, использование головок
SQUAREspot дает массу преимуществ как
в скорости, так и в качестве. Установка
использует 208 лазерных лучей, что обеспечивает
экспонирование цилиндра длиной 1 м за
2,5 мин. Возможно экспонирование в светлых
помещениях. Особое внимание разработчики
уделяют автоматизации всего процесса
изготовления цилиндра, а также возможность
печатать красками на водной основе.
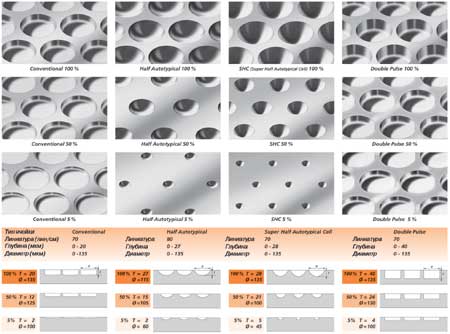
Различные
типы ячеек, которые способна воспроизвести
установка прямого лазерного гравирования
по цинку. Обозначения:
T - глубина ячейки в мкм, Ж - диаметр
ячейки в мкм
К основным достоинствам косвенного лазерного
гравирования можно отнести возможность
использования тех же цилиндров, которые
использовались, например, для электромеханического
гравирования. Тем самым достигается большая
гибкость процесса.
|
ЯУстановка прямого лазерного гравирования
LaserStar (MDC Max Daetwyler)
|
Прямое лазерное
гравирование
В
1992 г. компания MDC Max Daetwyler начала
разработку своей системы прямого гравирования
цинкового слоя LaserStar. Цинк был выбран
из-за его более низкой чем умеди теплопроводности.
В последствии к этим разработкам присоединилась
компания Spectron. Проведя исследования
в этой области, компания решила, что прямое
гравирование возможно только при использовании
очень стабильного лазерного излучения.
Для доставки луча к поверхности используется
оптоволоконный тракт. После ряда испытаний
компанией Spectron было предложено решение
об использовании двух 400-ваттных лазерных
лучей (каждый из которых генерируется
Nd:YAG Q-switch лазером с частотой 35
кГц), и последующего их объединения в
один поток 70 кГц. Это дает возможность
получить импульс, длящийся всего несколько
сотен наносекунд, что дает гарантию надлежащего
испарения гравируемого материала. Для
использования в гравировальной установке
потребовалось также разработать специальный
источник питания и систему охлаждения.
В итоге разработанная система позволяет
развить скорость гравирования, равную
70 тыс. ячеек/с (а при использовании двух
головок, как в современной модели LaserStar,
соответственно до 140 тыс. ячеек/с). При
этом стенки между ячейками имеют размеры
в несколько микрометров. Чтобы представить
такую скорость, можно привести небольшой
пример - гравирование 1 м2 поверхности
занимает всего 15 мин. Развертка осуществляется
по спирали. Q-switch синхронизирует пульсацию
лазера с частотой вращения цилиндра, в
то время как модулятор формирует лазерный
поток в зависимости от подаваемой информации.
Один импульс лазерного излучения формирует
одну ячейку. Профиль луча определяет тип
ячейки. Воздушный поток захватывает остатки
удаленного лазером цинка, после чего подвергается
фильтрации.
|
Оттиск с цилиндров, изготовленных
прямым
лазерным гравированием по цинку.
Увеличенный
фрагмент области полутонов )
|
Основной упор компания делает на структуру
ячеек, получившую название SHC (Super
Half Autotypical Cell). С помощью динамического
управления диаметром луча и импульсной
модуляцией (управлением мощностью) лазера
возможно получение ячеек переменного диаметра
и переменной глубины. При использовании
же традиционной растровой структуры Conventional
энергия лазера остается постоянной и автоматически
выбирается в зависимости от разрешения
гравирования.
Стоит также отметить возможность создания
макроячеек шестиугольной формы Master
Screen, синтезируемых перекрытием маленьких
ячеек. Подобная технология позволяет с
большой точностью управлять размерами
макроячейки, а значит, и точно дозировать
краскоперенос. Основная область применения
- печать на упаковке.
Так как ячейки имеют круглую форму, возможно
использование практически любых углов
растровой структуры, которые в свою очередь
определяются линиатурой. Оптическая система
линз позволяет использовать линиатуры
от 70 до 400 лин/см (170–1016 Lpi). Столь
высокие линиатуры могут быть использованы,
например, для устранения главного недостатка
глубокой печати - зубчатости штриха.
|
Различные типы
макроячеек,
получаемые
прямым лазерным
гравированием
путем комбини-
рования обычных
ячеек
|
Для осуществления прямого лазерного гравирования
необходимо предварительное гальваническое
нанесение на омедненную поверхность цилиндра
цинкового слоя (толщина такого слоя должна
на 15 мкм превышать максимальную глубину
ячейки и, соответственно, лежит в пределах
55 мкм). Эта операция производится на
установке Zincstar (MDC Max Daetwyler)
с достаточно большой скоростью - около
50 мкм за 45 мин, после чего цинковый
слой обязательно полируется. Применение
этого слоя дает возможность производить
гравировку лазером небольшой мощности.
Но так как цинковый слой достаточно мягок
и не обладает высокими прочностными показателями,
для получения заданной тиражестойкости
необходимы его дальнейшая очистка и хромирование.
Хромирование осуществляется электролитическим
способом при температуре 62°С. Прочность
полученной поверхности сопоставима с традиционным
хромовым покрытием меди. Толщина хромового
покрытия такая же, как и на обычном медном
слое - 6–8 мкм.
|
Результаты прямого
лазерного гравирования
|
Достоинство этого метода не только в
высокой скорости гравирования. Вторым
положительным аспектом является полусферическая
форма ячеек, благодаря которой возможно
наилучшее взаимодействие с дальнейшим
печатным процессом. Исходя из геометрии
полусферических ячеек, для обеспечения
необходимой оптической плотности на оттиске,
глубина ячейки уменьшена на 30% по сравнению
с полученной в процессе электромеханического
гравирования. При необходимости (для получения
более толстых красочных слоев) глубина
ячейки может быть увеличена путем выведения
лазера на полную мощность. Экономия краски
при применении SHC-структуры может достигать
20%, по сравнению с использованием технологии
электромеханического гравирования. Обычно
при использовании SHC останавливаются
на линиатуре от 70 до 90 лин/см. В этом
случае глубина ячеек будет колебаться
от нескольких микрометров в светах до
35 мкм в тенях, а диаметр - от 25 до 140
мкм соответственно. Такая форма ячеек
позволяет использовать более высокие скорости
печати.
Для повторного использования с цилиндров
механически удаляется цинковый и медный
слой.
Хотя подобная система Lasergravure стоит
примерно в пять раз дороже, чем традиционная
установка для электромеханического гравирования
(1,47 млн евро против 270 тыс. евро, например,
за систему Gravostar) и, соответственно,
требует гораздо больших инвестиций, в
итоге, по заявлению компании, позволяет
получить формный цилиндр, обладающий более
низкой себестоимостью. Среди причин можно
назвать:
- более высокую скорость гравирования.
Хотя, безусловно, сначала стоит задуматься,
будет ли востребована такая производительность;
- повышение качества оттисков, за счет
чего возможно удовлетворение самых требовательных
заказчиков, а значит, и получение дополнительного
дохода;
- уменьшение расхода краски и растворителя.
Некоторые типографии, уже использующие
подобные цилиндры, заявляют, что сумели
достичь 20-процентной экономии;
- уменьшение времени приладки в печатном
цехе.
|
Реализованые в установке HelioBeam
C2000 типы
ячеек (такие как на рисунке) разработаны
в
соответствии с главным требованием
косвенного
лазерного гравирования - минимизацией
эффекта
подтравливания, чему служит их необычная
форма
|
Что ждет глубокую печать в будущем?
Хотя
электромеханическое гравирование до сих
пор пользуется большой популярностью,
по оценкам многих экспертов, доля оборудования,
использующего лазерные технологии (как
и непосредственно прямое лазерное гравирование,
так и с использованием масочной технологии)
будет постепенно расти, но, конечно, не
так быстро, как это происходит, например,
в офсете.
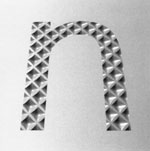 |
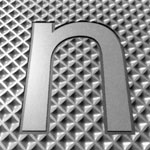 |
Принципиальное отличие косвенного
лазерного гравирования
от электромеханического - возможность
при необходимости
создавать более четкие края букв за
счет дополнительной
контурной обводки (справа) или неполного
воспроизведения ячеек (слева)
|
Другим очевидным направлением развития
глубокой печати является использование
пластиковых цилиндров. Уже сейчас в качестве
основания для небольших формных цилиндров
иногда используются более легкие алюминий
и пластик вместо традиционно используемой
для этого стали.
Если же попробовать заглянуть в более
отдаленное будущее, то с большой долей
вероятности возможна успешная реализация
прямого лазерного гравирования на меди,
на котором уже давно сосредоточены усилия
многих производителей формного оборудования
глубокой печати.

|